Versatility
In Power Fabric, we are able to adapt to many different techniques of textile production. In addition to our knitting and weaving capabilities, we have a large collection of supporting machines such as dyeing mill, warping machine, washing and drying machine, stentering machine, flame lamination machine and yarn twisting machines. After the specifications of the order is confirmed, our laboratory and RND department carefully finalizes every detail such as color, weight, width and the touch. The smooth connection between our departments is carefully planned and executed using the latest computer technology to minimize defects or imperfections.
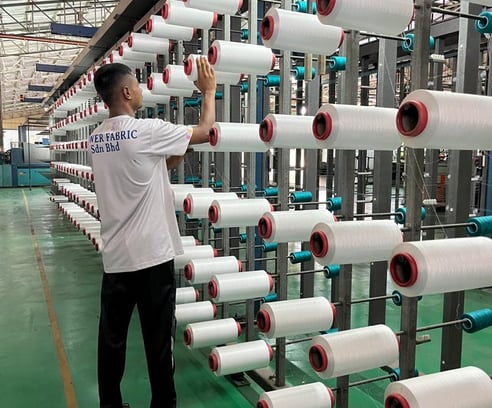
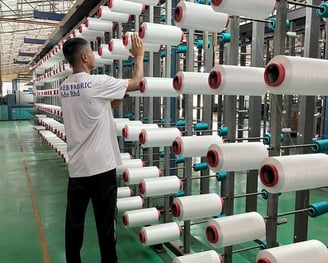
Warping Machine
Warp and weft are the two basic components in weaving to transform thread and yarn into textile fabrics. The vertical warp yarns are held stationary in tension on a loom (frame) while the horizontal weft (also called the woof) is drawn through (inserted over and under) the warp thread. In the terminology of weaving, each warp thread is called a warp end; a pick is a single weft thread that crosses the warp thread. Warping refers to the process of arranging yarns or threads lengthwise on a loom. It ensures that the threads are properly aligned and tensioned before the weaving processes. After the draw in process, beams are moved to either Water Jet or Air Jet weaving machines depending on our production schedule.
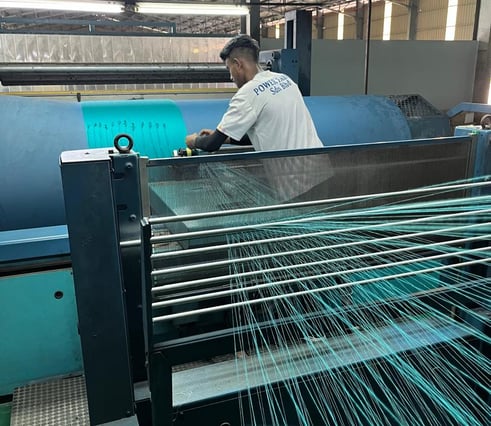
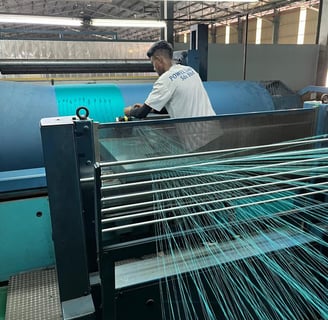
Washing and Drying Machine
Textile wash is the technology used in textile industry to modify outlook, control size, enhance comfortability and create new fashionable look of any fabric or textile product or garments or apparels. Apart from cleaning and removing bad odor, textile wash creates special impact on garment's status. Drying is defined as a process where the liquid portion of the solution (moisture content) is evaporated from the fabric. This is done after de-watering of fabric. The water dispersed in a textile material by a chemical–physical process is eliminated by the action of hot air, which makes the water evaporate.
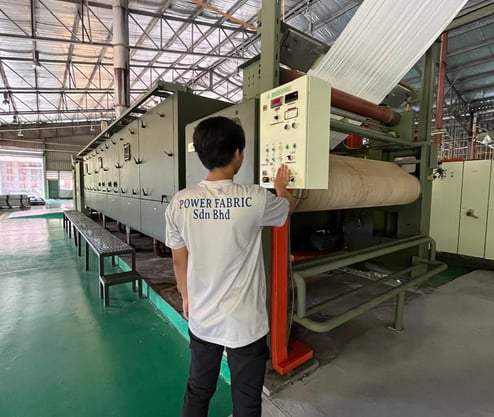
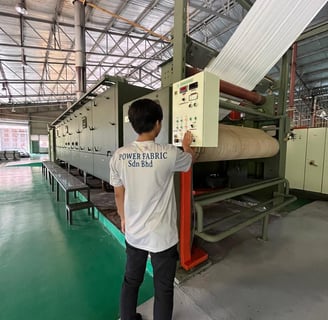
Knitting Machines
Knitting is a method for production of textile fabrics by interlacing yarn loops with loops of the same or other yarns. Using highly automated equipment, we can produce various type of knitted fabric. Our variety of machines can produce all types of knitted fabrics such as single jersey, jacquard, double jersey and many more. Single jersey fabric is very breathable and comfortable to wear for a very long time. The double jersey is knitted using 2 sets of needles. Also known as Ponte di Roma, double jersey is a reversible fabric. That means it can be double face or double reverse.
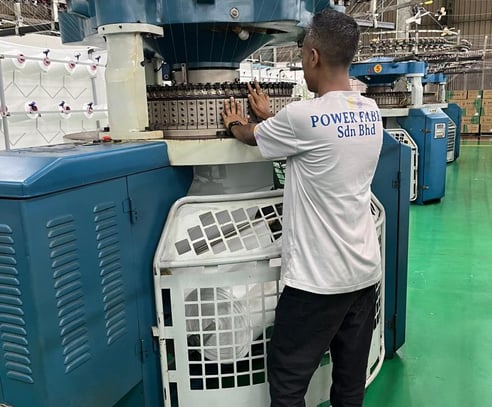

Weaving Machines
Weaving is a method of textile production in which two distinct sets of yarns or threads are interlaced at right angles to form a fabric or cloth. We produce variety of woven fabrics thanks to our Water Jet and Air Jet weaving machines which enables us to produce according to the demanded quality from our esteemed customers. An air jet loom, a type of shuttleless weaving machine, uses a jet of compressed air to propel the weft yarn (or filling yarn) through the warp shed, allowing for high-speed and efficient fabric production. Water jet loom is used to make water-repellent fabric materials, primarily multi-filament synthetic yarns. It is also used to make light and medium-weight fabrics with standard characteristics.
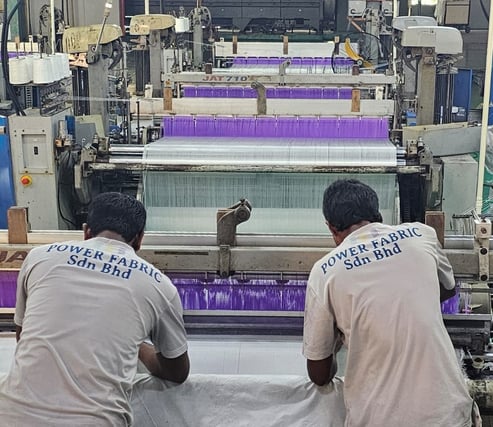
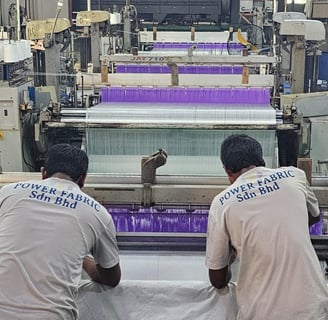
Stenter Machine
A stenter machine is a piece of equipment used in textile finishing that uses a chain or frame to hold the fabric edges and apply heat and tension. It is a finishing method used on textiles to stretch the fabric and control its dimensions during the drying and heat-setting process. It serves multiple purposes, including heat setting, drying, and applying various chemical treatments. This may be achieved through the use of certain attachments such as padding or coating. Eventually, the stretched sheet is pulled off at a specific speed by a second set of rollers. At the delivery end, the edges are released by the stenter pins or clamps that were holding it.
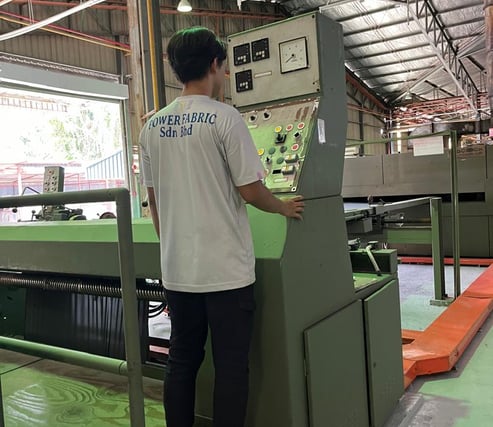
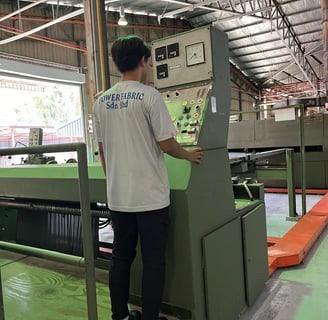
Yarn Twisting Machines
It is a textile machinery which twists multiple strands of yarn into one strand. The spindle outside the twister body is connected with the motor output shaft of the circuit part, and the front end of the spindle is equipped with connectors, which correspond to the tap-changer. The bobbins are looped on the insert in the horizontal form, and the ply yarn pulls the bobbin from the side and turns back. In order to reduce the end breakage caused by excessive tension during unwinding of single yarn, a conical cylinder is used to tightly cover the insert spindle, and the single yarn is pulled out axially from the respective end of the tube to realize the coalescence in the feeding frame.
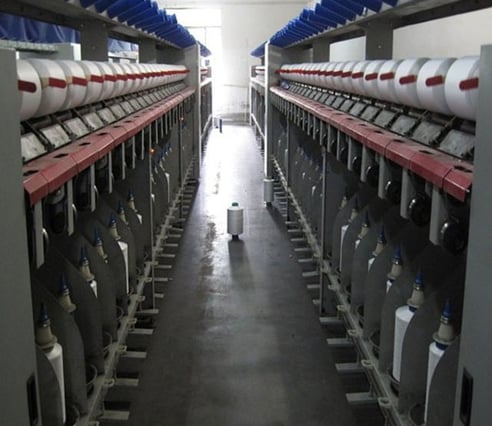
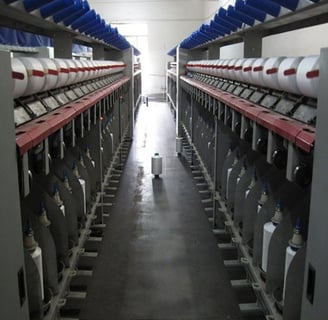
Flame Lamination Machine
A flame lamination machine uses an open flame to heat one material, then quickly presses it against another to create a strong, durable bond, eliminating the need for adhesives or solvents. The machine uses a line-gas-burner to heat the surface of a material, typically a foam like PUR, until it becomes pliable and forms an adhesive film. The heated material is then pressed against another material, such as artificial leather, fabric, or another foam, creating a strong, uniform bond. Unlike traditional lamination methods, flame lamination doesn't require any adhesives or solvents, making it a clean and efficient process. Flame lamination is a relatively fast process, making it suitable for high-speed production lines.
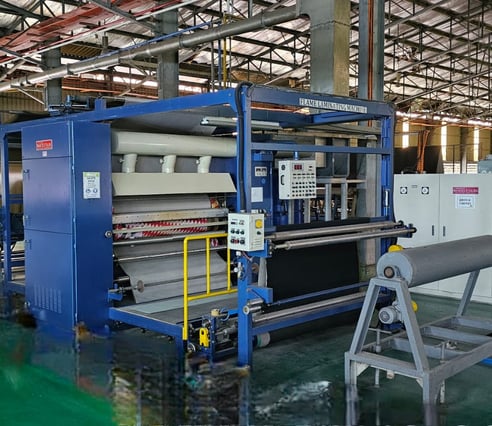
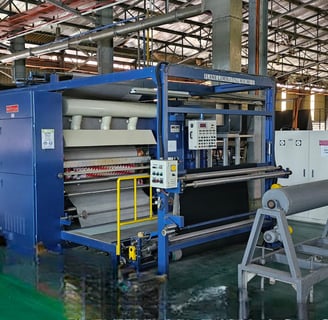
Yarn Sizing Machine
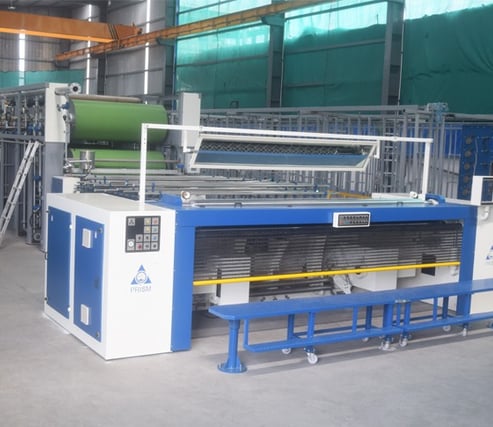
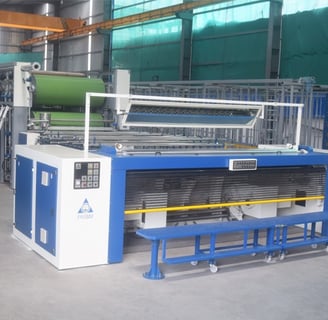
Yarn sizing is a process of applying a sizing agent to the warp yarn to improve the strength of the warp yarn in order to resist the mechanical stress applied to the yarn during weaving. There are different kinds of sizing agents such as polyvinyl alcohol, starch and acrylic-based sizing agents. The objective of sizing is to coat the warp yarn with size paste. This helps the yarn to withstand the weaving tensions, by imparting additional strength. The sizing also helps to cover the protruding fibers in the yarn thereby preventing yarn breakage in weaving due to entanglement of neighboring ends. Adhesive can be single shot sizing chemical or a blend of multiple chemicals to achieve desired properties.
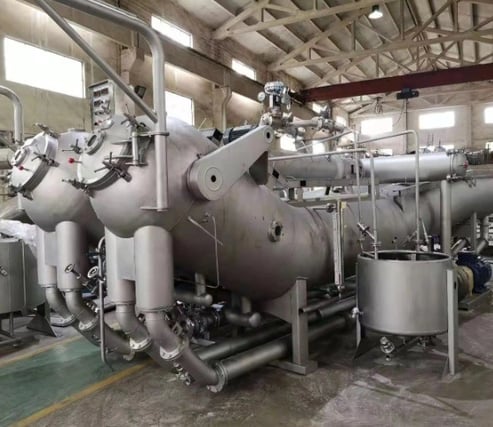
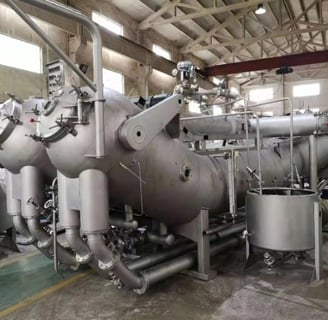
Dyeing Machines
Dyeing is the application of dyes or pigments on fabrics with the goal of achieving color with desired color fastness. Dyeing is normally done in a special solution containing dyes and particular chemical material. Dye molecules are fixed to the fiber by absorption, diffusion, or bonding with temperature and time being key controlling factors. The bond between the dye molecule and fiber may be strong or weak, depending on the dye used. Our Jet Dyeing Machines use high-pressure jets of dye liquor to circulate through fabric, ensuring uniform dye penetration and color fastness, making it an efficient method for dyeing various textiles.